Sewing machine breakdowns and their elimination. Problems with the sewing machine and how to fix them. Bottom thread break
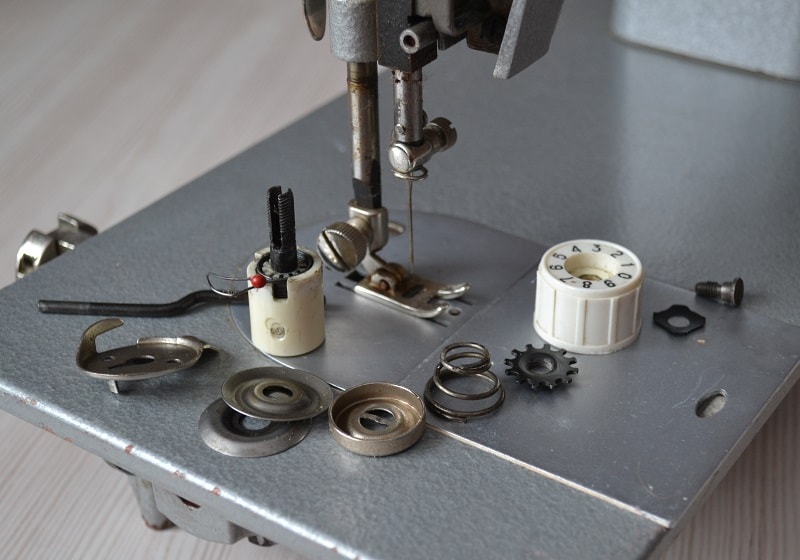
Basic, typical faults and problems with sewing machines: bad line, thread breakage, needle breakage.
Skipping stitches in a line sewing machine and overlock appears if a low-quality thread or needle of the wrong thickness is used. The size of the gap between the needle and the nose of the shuttle (loopers in an overlocker) also affects this.
Defects such as “bias stitch” and broken upper and lower threads can usually be eliminated by adjusting the tension of both threads. But, if, after adjusting the tension, stitch defects do not disappear, then you will have to adjust the interaction of the shuttle stroke and the needle, the mechanism for advancing the fabric, etc. This is especially typical for the Chaika sewing machine. Moreover, if the installation parameters of the “Seagull” shuttle are off, then it is quite difficult to make such an adjustment yourself. But mostly eliminate sewing machine malfunctions and problems can be done by correctly adjusting the thread tension, replacing the needle, lubricating and cleaning the machine.
This comprehensive approach to the problem is that very often one component that is not working properly can lead to poor performance and even damage other parts. During the tests described here, it turns out that, for example, some item is for exchange. This refers to components that are used or simply destroyed due to improper use of the machine. Our service will notify you when such parts are replaced. You will need to pay extra for this, so your consent will be required.
Sewing machine lubrication and lubrication
Without it, we do not replace used items. If we already know that all the components are in good condition and working properly, our technician will perform the service work on the sewing machine. All moving parts are lubricated with Vaseline oil. This also applies to places that are inaccessible without a cover, making it difficult to take care of yourself.
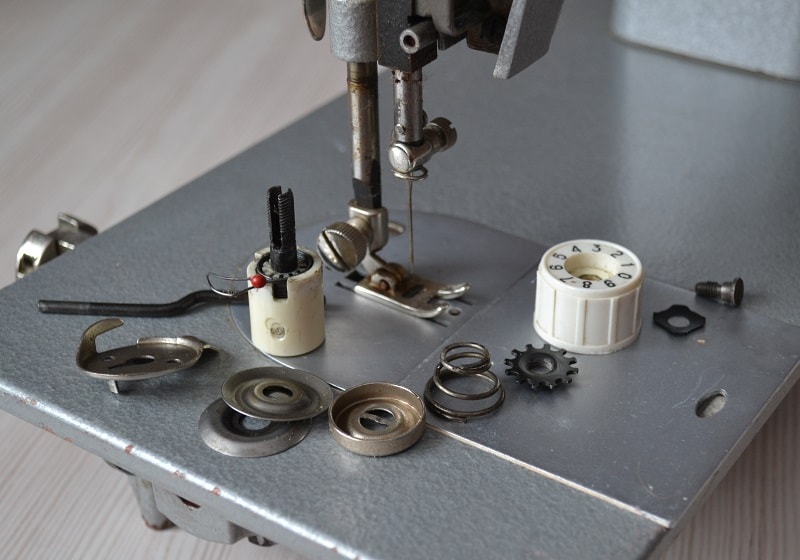
After disassembly, the tensioner is incorrectly assembled upper thread.
- Incorrect threading.
- Poor quality threads.
- The thread number does not match the needle number.
- The spring of the bobbin case lock has weakened.
Inside the bobbin case you can find a very small screw, and if you unscrew it, the lock mechanism can be removed and you will find a long spring. Try to stretch this spring slightly, but it is better to buy a new bobbin case.
- There are nicks and burrs along the path of the thread to the needle.
Carefully follow the path of the thread and, after detecting nicks, remove them with a small needle file. In older Podolsk-type machines, there may be thread cuts on the tensioner rod. Disassemble the tensioner and inspect the rod; if there are such cuts, remove them with sandpaper.
In addition, the modes in the machine are thoroughly lubricated. While any of us can do it ourselves, lubricating a machine is more of a job for professionals who have a hand lubricant with the appropriate properties. After these operations we are confident that any gears, couplings, drive components, shafts, etc. will operate with proper slippage. It is important that after about 5 years the lubricant oxidizes, so it is important to remember to return the lubricant at least once every 5 years.
Sewing machine sewing and sewing machine testing
Once the machine has already been checked and oiled, we will begin making adjustments. Always replace the needle in the machine with a new one. We want all adjustments to be correct and done with the straight needle attached. Even a little curling can ruin the effect. And the quality of stitching and appearance is very important to us, so we check it with the right precision.
2. Reasons for breaking the bottom thread


The reason for the bottom thread breaking may be a low-quality thread, for example, cotton thread from Soviet times.
- The screw that presses the spring (plate) on the bobbin case protrudes excessively.
The tension of the lower thread is often adjusted, and sharp nicks appear on the screw head. The lower thread, wrapping around the bobbin case, clings to them and breaks off.
- The lower thread tension in the bobbin case is too tight.
- There are nicks on the edges of the bobbin.
The thread gets between the bobbin and the walls of the bobbin case and breaks. Change bobbins as soon as the first nicks or chips appear.
- The edges of the bobbin are bent, there are gouges from the needle and nicks.
The last stage of checking the machine at the service is to perform test transitions. We guide them through three different types of materials. Medium thickness fabric rough fabric, knitwear . The machine sews different stitches on each of them. We attach the results of the work, that is, test sewing, to the machine that we send to you. It is important to note that we only complete testing when the stitching obtained on all materials is correct.
The procedures described here are tested by our experienced specialists for at least 2-3 hours. Usually there is enough time to restore the machine to full functionality. And what is very important, sewing on such a machine will be more enjoyable and relaxing, because the risk of some serious error is minimized. The price of this service and many others.
3. Looping the lower and upper threads. Bad line

The thread on the spool and bobbin is unevenly wound. Do not wind the thread onto the bobbin by hand; use a special device for this. Evenly laying the thread on the bobbin ensures the same uniform thread flow. Hand-wound thread can get caught in other turns and pull the upper thread more than it should. As a result, loops appear at the bottom.


Dirt or fuzz or thread trimmings have gotten under the leaf spring of the bobbin case.
- A slot has formed under the leaf spring on the bobbin case. This happens after many years of intensive use of the sewing machine. You should not fix bobbin case malfunctions yourself, except for cleaning and adjusting the thread tension. The best solution to troubleshoot a bobbin case is to buy a new case.
- Weak tension on both threads.
- Strong tension on both threads.
4. Poor fabric advancement

Weak foot pressure.
- The sole of the foot is skewed, and it does not press the fabric with its entire surface.
- The teeth of the rack are dull.
- is set to embroidery mode or the teeth of the feed dog are too low and do not catch the fabric well. The correct position of the teeth when sewing medium-thick fabric: with the maximum rise of the feed from the needle plate, the teeth should rise completely, but not higher than the height of the teeth. Their position too high will create a “fit” in the fabric or tighten it.
5. Reasons for needle breakage

The needle number does not match the thread number or fabric thickness.
- The needle is bent.
- The needle is not inserted into the needle bar all the way.
- The needle does not pass through the center of the needle hole of the plate. The needle must pass exactly in the center of the hole in the needle plate. Make sure that the needle does not touch the rail while using the sewing machine. Incorrect needle position may be caused by a bent needle bar.
- The needle bar position is set too low or high.
- Incorrect sewing. While sewing, do not pull the material by hand; find the reason why the machine does not advance the fabric well. Adjust the presser foot pressure on the fabric.
6. Skipped stitches

The needle is too high when it meets the nose of the hook and it does not catch the needle loop. See Setting up the shuttle of the Chaika sewing machine.
- The needle is bent or the needle point has become dull.
A curved needle can be identified in the light by twisting it on a flat and dark plane.
- The needle is not installed all the way or incorrectly, on the wrong side.
- Using a needle type that is not intended for this sewing machine. Often, in household sewing machines industrial needles are used. They do not have a cut on the flask and are absolutely not intended for such machines.
- The settings for the interaction of the needle and the shuttle are misaligned.
If the foot drive is, one might say, a complete antique, then the manual drive can be used, especially for those starting to learn to sew. Read this article to learn how to repair this device yourself.
The main malfunctions and malfunctions of these sewing machines, as a rule, are not related to its adjustment. Sometimes it is enough to install the needle correctly, replace low-quality threads, select the correct tension of the lower and upper threads, and the machine will work perfectly again.
A broken needle on a sewing machine is a sign that it requires “serious” tuning or adjustment. But, often, setting up the sewing machine is not required; it is enough to stop pulling the fabric while sewing. The second common cause of needle breakage is sewing thick fabrics that are not intended for sewing on this model of sewing machine.
Skips occur due to the fact that the nose of the shuttle “meeting” the needle does not pick up the upper thread from it. Either it is located far from the needle (large gap), or the upper thread loop is formed too early or late, or is too small. That's all the reasons, simple, isn't it? All that remains is to find out why this happens and how to eliminate these malfunctions.
The line loops, which means that the top thread “slows down” during movement and an excess of it appears. There are many reasons for this, ranging from the uneven thickness of the thread itself to the shuttle stroke. Start by carefully tracing the path of the thread. Perhaps it just clings to the fine notch of the thread guide.
It's rare, but sometimes you can find foot-operated machines. The best solution is to install an electric drive on the machine instead of repairing the drive. This is done quite easily and anyone who has a screwdriver can install it with their own hands. But, if you need recommendations on how to repair or adjust the foot drive, this article is at your service.
Sewing machine faults and problems It will be easier to fix if you understand how the sewing machine works and which part is used for what. Study carefully the structure of your machine according to the instructions or using our article.
The machine must be lubricated at least once a year. But don’t overfill it with oil. Oil tends to dry out over time, and the resulting clumps of dried oil can cause some sewing machine malfunctions.
The bobbin is that inconspicuous detail that no one pays attention to. And it is this that causes many problems and malfunctions of the sewing machine. You can disassemble the entire machine without finding the reason for the “looping” of the stitching. And as soon as you replace the bobbin with a new, smooth and light one, the stitching will be even and beautiful.
A sewing machine needs lubrication like oil for your car engine. But we take care of the car and wash it with shampoo almost every week. Why not then wipe the body of the sewing machine from dust, clean its internal mechanisms with a brush so that they are clean and dry, without traces of oil and thread frays.
— To prevent malfunctions in the operation of sewing machines, the machine should be kept in a dry place, away from heating appliances.
— Threads and sewing needles vary in thickness and have their own numbers. There are rules that sewing needles and sew this or that fabric with threads.
Thin fabrics (cambric, chiffon, crepe de Chine, etc.) are sewn with cotton threads No. 100-80, needle No. 90; calico fabric, and staple - with threads No. 80-60, needle No. 90; light woolen fabrics and heavy ones made of chemical fibers - with threads No. 60-40, needle No. 100; heavy woolen fabrics - with thread No. 40, needle No. 110; coarse cloth, beaver, burlap are sewn with thread No. 30-10, needle No. 120.
True, it happens that the threads cannot be matched to the tone of the fabric and the required thickness, then there is no needle as required... In these cases, you can sew with the most common needles No. 90 and threads No. 40.
— When you start sewing, the thread guide and needle should be at the top. Place the fabric under the presser foot, lower it down, lower the needle, make 2-3 injections manually, rotating the handwheel towards you.
— Without helping the machine, pulling the material with your hands, it may bend or break, and the stitching will be uneven.
- But the work is finished. Raise the presser foot, pull the fabric back and to the left, cut the threads, leaving ends 6-7 cm long. Place a cloth under the foot, lower the foot with the needle to the bottom position.
Hold the flywheel and release the idle screw by turning it towards you. Remove the belt if the machine is mechanical, and unplug it if the machine is electric.
— But sometimes the machine stops sewing: the thread breaks and loops, the stitching is uneven, the fabric does not advance... We need to find problems with sewing machines and fix them.:
1. Sewing machine malfunction - upper thread breaks. The needle is not installed correctly (inserted too high or too low). Thread and needle numbers do not match. The needle is too sharp or dull or bent. The thread has knots or its thickness is uneven. The thread tension was too high.
2. Sewing machine malfunction - lower thread breaks. Maybe from too much tension. The bobbin case is not installed correctly. The bobbin is bent or has burrs. The threads on the bobbin were wound incorrectly. The stroke body is dirty or not lubricated. The bobbin case is clogged.
3. Problem with sewing machines - the upper thread gets tangled. They forgot to thread it into the “plates” (regulator) of the upper thread or its tension is too weak. The thread thickness does not match the needle number.
4. Problem with sewing machines - the fabric does not advance. The teeth are lowered too low or, conversely, they are raised too high. Weak presser foot pressure. A lot of dust has collected under the needle plate.
5. Problem with sewing machines - the thread forms loops. The thread is not threaded correctly. Weak upper or lower thread tension. The thread thickness does not match the needle number.
6. Problem with sewing machines - uneven stitching . The screw in the bobbin case is not screwed in tightly enough. The screw threads are clogged. The zigzag mechanism is not completely turned off.
7. Problem with sewing machines - cutting through fabric. Strong pressure presser foot. The needle is too thick, the stitch is too fine, or the thread is too thick. The needle is not inserted firmly enough. The needle is not installed correctly in the needle bar. The needle is dull or bent. The thread number does not match the needle thickness. The material is too thick. There are sharp burrs on the teeth, needle plate, and foot.
8. Malfunction of sewing machines - material is “picked up”. Incorrect tension on one of the threads. Weak or strong presser foot pressure. The sole of the paw has worn out. Too much tooth lift. The needle holder is too short.
9. Problem with sewing machines - heavy running of the machine. The old grease has thickened. The machine is poorly oiled. Threads are wound between the bushing and the flywheel of the machine.
All these problems in the operation of sewing machines are minor, and you can easily fix them at home yourself.
- Review of the smart robot vacuum cleaner ILIFE A9s: cleans, washes, builds walls. What's in the box
- German technology in Wasser Kraft faucets
- German technology in Wasser Kraft faucets
- About the manufacturer MILARDO Advantages of the Milardo® brand
- Subtleties of choosing carbon heaters Carbon infrared heater
- Infrared carbon heater: pros and cons
- How not to pay for heating if the apartment has cold radiators